Mr. Chikayuki Nagata
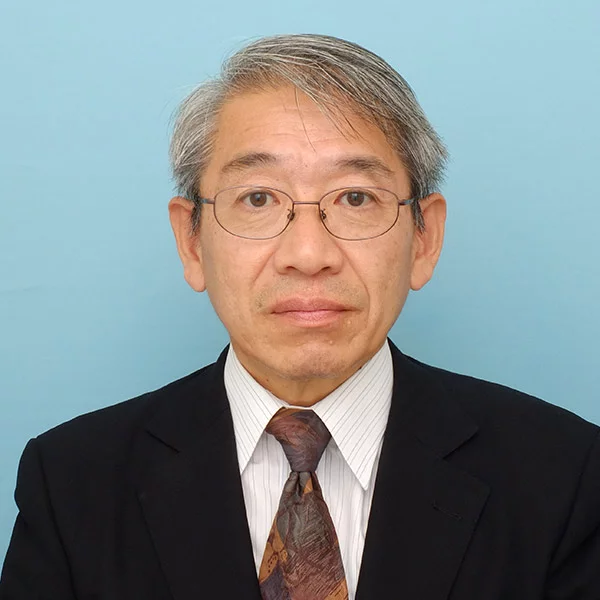
Business Position: Senior Manager
Company: Mitsubishi Heavy Industries Power Environmental Solutions
Year of Birth: 1959
Years in Industry: 38
Nationality: Japanese
Phone: +81 80 2424 0827
Email: chikayuki.nagata.c5@mhi.com
Mr. Chikayuki Nagata is a mechanical engineer and joined Mitsubishi Heavy Industries, Ltd. (MHI) in April 1985, after receiving his bachelor’s (1983) and master’s (1985) degrees in mechanical engineering from Nagoya University, and he was assigned to an environmental equipment division in Kobe, and there he was involved in many projects as a person responsible for the detailed design, basic planning and development of ESP.
As the detailed design engineer of the ESP, the most important project he was involved was the hot-side ESP, which was installed on the upstream side of the air pre-heater of a 1000 MW coal-fired power plant. It requires the selection of a material that can withstand use at high temperatures of 400 degrees Celsius, and a design that takes large thermal expansion into consideration.
One of the key projects he experienced as an ESP basic planner was the installation of a wet ESP in Austrian power station fueled with high sulfur contained heavy oil. In the gas quenching process of a wet desulfurization system to remove SO2 from power plant flue gas, partially oxidized SO3 combined with the water to create very fine sulfuric acid mists, and the mists were discharged from the stack as so-called bluish plume, causing visible smoke to become a problem. To remove the sulfuric acid mist, it was decided to install a wet ESP, which had already been proven in Japan. This was the first wet ESP installed in a boiler plant in Europe.
In a project in which dry ESPs were installed to existing power station in Chile, he was responsible for the basic planning and then worked as a technical coordinator at the site for about a year, getting experience in site management. Using that experience, he later worked as a project manager for several ESPs (or ESPs and ash handling units) for overseas large-scale coal-fired power plant projects.
Alongside working on these actual projects, he was also involved in research and development work. The development of high-velocity ESP (HV-ESP) is a typical example. The result was later realized in tunnel ESP with large air volume and high velocity flow, which was installed in automobile tunnels to remove particles such as unburned carbon emitted mainly by diesel vehicles.
For 2 years from 1998, he was the team leader of the construction planning department for environmental equipment, including ESP.
In 2000, he returned to ESP’s design and planning department, where he worked on technical negotiations with clients, mainly on projects for overseas markets. During this period, he also served as a lecturer in charge of ESP education in a project in which the Japanese government invited personnel from power plants in developing countries to Japan every year for education.
During the period from October 2006 to March 2009, as part of the personnel exchange program within MHI, he went to the power systems division in Nagasaki to work on improving the procurement capability of ESP as a boiler auxiliary. During this period, he also considered adopting a competitor’s ESP in three projects in Saudi Arabia, Mexico, and Indonesia before finally adopting an ESP from MHI’s environmental equipment division. This successfully created a win-win relationship for both the power systems and environmental equipment divisions. Then, in April 2009, he returned to the environmental equipment division in Kobe again.
Haramachi Thermal Power Station of the Tohoku Electric Power Company was the most severely damaged coal-fired power plant when the tsunami was caused by the Great East Japan Earthquake that occurred in the Pacific Ocean near Japan on March 11, 2011. The plant’s ESP was to remove and completely replace the existing equipment, and he was assigned as the project manager for the replacement of Unit 1’s ESP and ash handling equipment. It was a rush project to complete the ESP of the 1000 MW plant in 10 months, from the start of construction to the start of boiler firing, but the project was successfully completed without any accidents or disasters.
In October 2015, two of Japan’s leading ESP manufacturers, Mitsubishi and Hitachi, agreed to merge their operations, and a new company was established with headquarters in Yokohama. With the launch of the new company, he was involved in the integration of Mitsubishi and Hitachi ESP technologies at the Yokohama headquarters.
He returned to Kobe in May 2021 and now collects and analyzes technical information, including patents, on his own and other companies’ technologies related to ESP in general.